Natural Rubber is considered an “Essential Commodity” (designated in 2020) in the EU since it is widely used in many applications and cannot be substituted by synthetics. The world production is confined to South East Asia and West Africa, and the industry is controlled by China, making it subject to political instability from time to time. This has a profound effect on its commodity price which fluctuates considerably from year to year.
Traditionally, natural rubber is derived from the tree Hevea braziliensis, a species introduced to Asia from Brazil, as its name suggests. Most of the plantations in Asia are established from a reduced gene pool, with the consequent dangers associated with limited genetic diversity, and there is a perennial possibility of disease, (particularly fungal disease) spreading rapidly through the growing regions and destroying a vast industry. This was the case in Brazil at the beginning of the twentieth century.
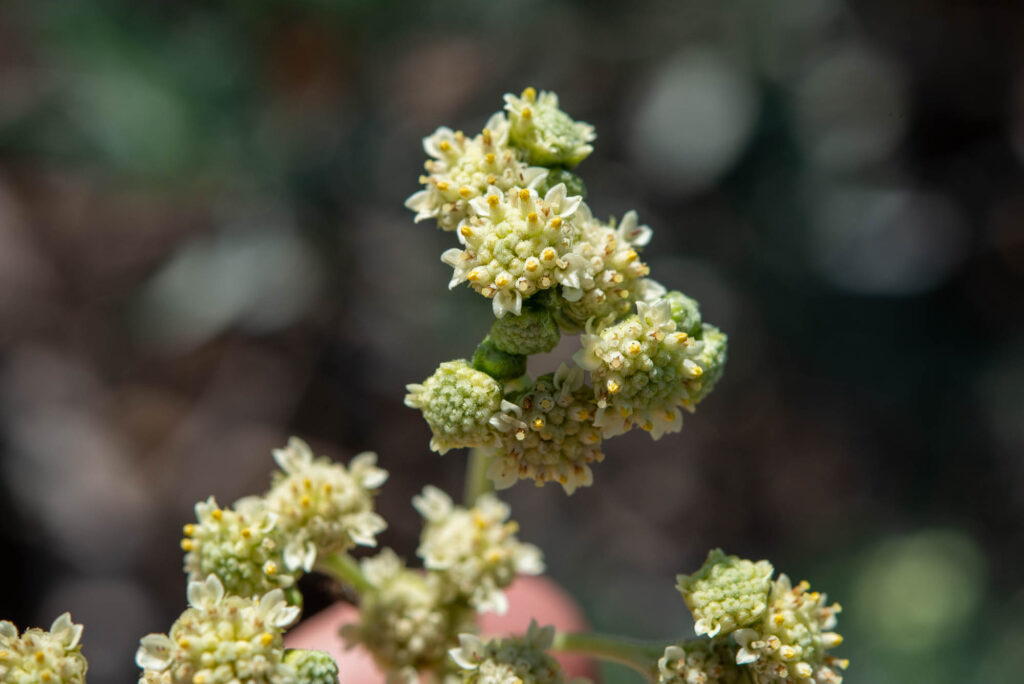
In addition to this, the world’s appetite for substituting large areas of rain forest for mono-cropped and mono-clonal tree plantations is a thing of the past, and room for expansion to meet an ever growing demand for natural rubber is limited. From the time of planting, Hevea takes at least 7 years to the production of latex, the pre-cursor to natural rubber, and research for new clones is thus slow. The days of rubber plantation agriculture in South East Asia must be limited, since it is labourious and manual, while the demand for the product increases at about 4% per year.
Scientific development of an alternative, non-allergenic and mechanizable source began in the USA during WW2 when access to the South East Asian plantations was blocked by Japan. The target plant to produce latex and rubber products, largely for tyres, was (and remains) Parthenium argentatum (common name: Guayule). This is an American shrub, occurring in the deserts of N. Mexico and the Southern USA.
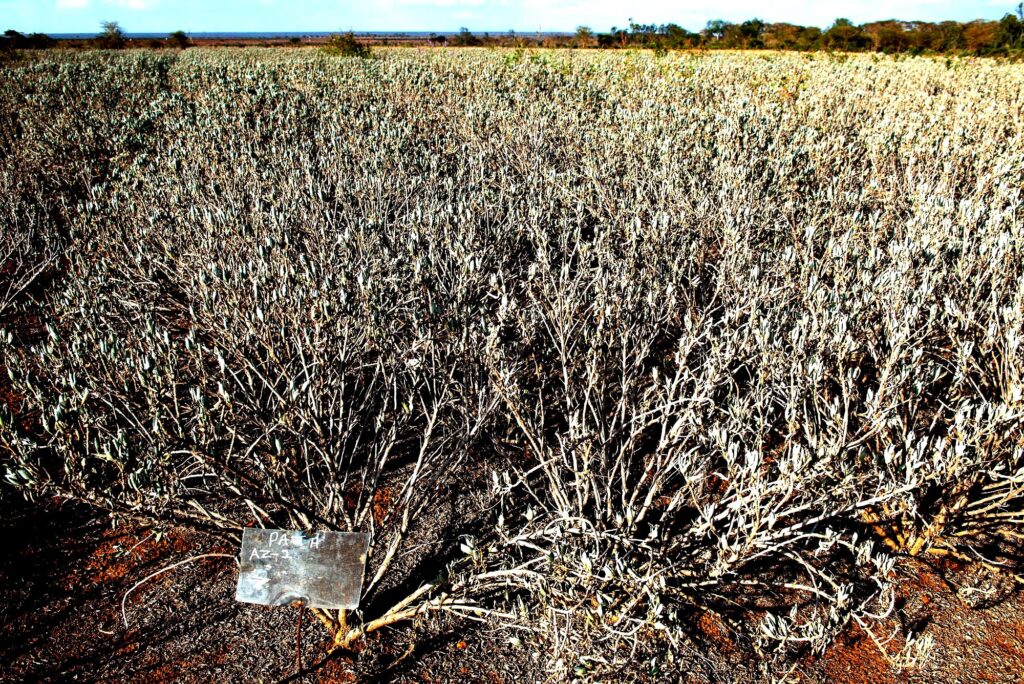
Much research has been applied to its development since the Oil Crisis of the ‘70’s, when prices for synthetic rubber rose sharply along with the price of oil, and today two large tyre companies and several smaller ones continue breeding programmes and production plans for Parthenium, largely centred in the US.
In 2019 Natural Rubber Kenya imported seed of 26 varieties of Parthenium argentatum from the US, through KePHIS, and began agronomic trials in Laikipia (central Kenya). Simultaneously, we began a correspondence with a couple of agricultural advisory and research organisations to help us in the matter.
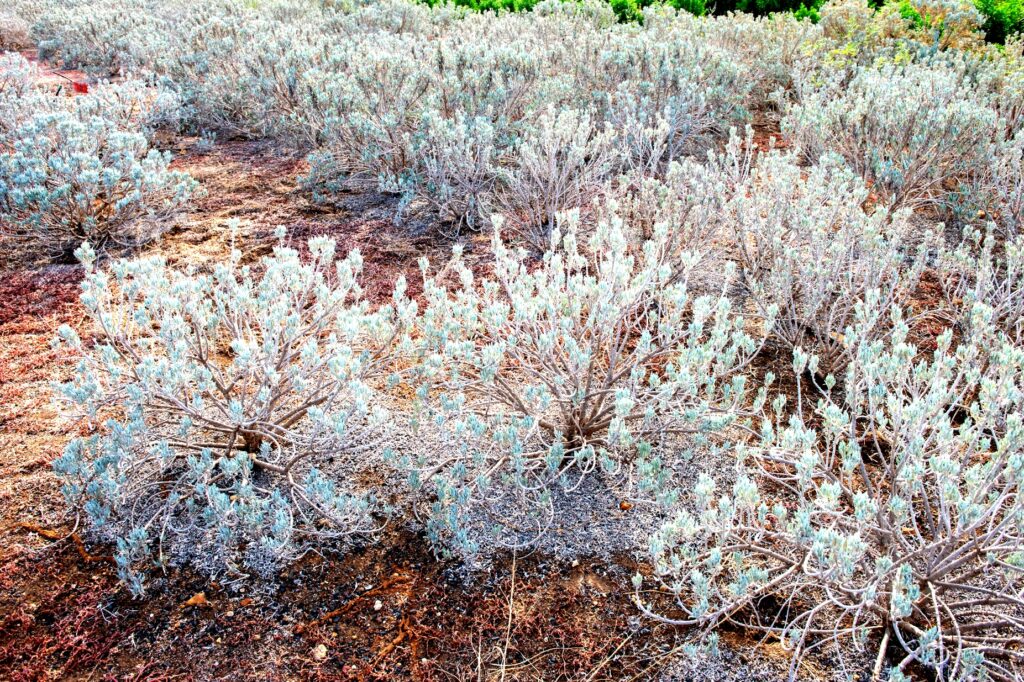
Of the 26 accessions of seed we trialled, four have shown themselves to be exceptional in our conditions. Rubber content is high, growth of this desert plant is excellent, and no pests or disease have been recorded in 3 years of continuous trials. The plants have responded very well to our climatic conditions, with no recourse to irrigation or to pesticides and fertilizers (except natural rock phosphate at planting). In our conditions we believe that cropping can begin 18 months after transplanting, and that the plants can be cropped every year after that for as long as 10 years. This compares with the US and southern Europe, where cropping begins after two years, and the plant life expectancy is seven years.
The company has started in 2024 to plant 50ha in Northern Kenya which will be followed by another 100ha / 150ha in the course of the next two to three years, so that a consistent amount of biomass is available for all trials of extraction and manufacturing.
Guayule Kenya Limited (the company trading as “Natural Rubber Kenya’) signed an NDA with GuaTecs SAS proceeded with plans to transform trials into a commercial venture as a partnership: Natural Rubber Kenya and Ol Maisor Farm will produce the plant, and GuaTecs SAS will build a joint-owned process plant to extract natural rubber, and to utilize the by-product of the extraction process to make termite-resistant chip board for the local market.
Guayule Kenya is also partnering with another Kenyan company for the production of medical items (gloves, condoms, catheters and the like). The East African market is very promising for these items as there is no local manufacturer and the Kenyan company wants to fill this vacuum.